生产中经常遇到一些铸件,因工艺分型面位置限制,厚大部位不得不放置在铸型上部,为防止这个部位出现“缩于“,“缩松”可采用以下措施;①在厚大部位开置内浇道,使得这个部位能有足够的高温铁水补缩;②厚大部位下方和侧面放置一定厚度的外冷铁,如果条件可行,插入内冷铁也可达到目的;③在不影响铸件材质强度、硬度的要求下,适当提高铁水碳当量,也是 可行的办法之一。
中大型大型铸件的生产实践中,不能完全依靠加大冒口尺寸和数量来达到补缩的目的。
2、铸件变形、几何尺寸超差
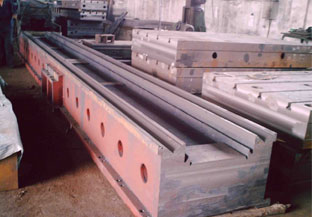
铸件成型的理论金属液态成型常称为铸造,铸造成形技术的历史悠久。早在5000多年前,我们 的祖先就能铸造红铜和青铜制品。铸造是 应用较广泛的金属液态成型工艺。它是 将液态金属浇注到铸型型腔中,待其冷却凝固后,获得一定形状的毛坯或零件的方法。机床床身铸件在机器设备中液态成型件所占比例很大,在机床、内燃机、矿山机械、重型机械中液态成型件占总重量的70%~90%;在汽车、拖拉机中占50%~70%;在农业机械中占40%~70%。液态成型工艺能得到如此广泛的应用,是 因为它具有如下的优点:
1)可制造出内腔、外形很复杂的毛坯。如各种箱体、机床床身、汽缸体、缸盖等。
2)工艺灵活性大,适应性广。液态成型件的大小几乎不限,其重量可由几克到几百吨,其壁厚可由0.5mm到1m左右。工业上凡能溶化成液态的金属材料均可用于液态成型。对于塑性很差的铸铁,液态成型是 生产其毛坯或零件的方法。
3)液态成型件成本较低。液态成型可直接利用废机件和切屑,设备费用较低。同时,液态成型件加工余量小,节约金属。 但是 ,金属液态成型的工序多,且难以精确控制,使得铸件质量不够稳定。与同种材料的锻件相比,因液态成型组织疏松、晶粒粗大,内部易产生缩孔、缩松、气孔等缺陷。其机械性能较低。另外,劳动强度大,条件差。 有优良的机械、物理性能,它可以有各种不同的强度、硬度、韧性配合的综合性能,还可兼具一种或多种特殊性能,如耐磨、耐高温和低温、耐腐蚀等。铸件的重量和尺寸范围都很宽,重量较轻的只有几克,较重的可达到400吨,壁厚较薄的只有0.5毫米,较厚可超过1米,长度可由几毫米到十几米,可满足不同工业部门的使用要求。
大型机床床身作为我们 日常生活中经常会用到的产品,主要受以下四个因素影响。
一、铸铁件设计工艺性。在进行设计的时候,除了根据工作条件和金属材料性对铸件几何形状和尺寸进行确定,还要根据铸件工艺特性角度和铸造合金来对设计合理性进行考虑 ,以避免铸件出现变形、开裂和成分偏析等缺陷。
二、铸造工艺要合理,就是 根据铸铁件的结构、尺寸和重量来选择合适的造型、造芯方法。并且要对冷铁、冒口和浇注系统进行合理设置,以此保证铸铁件的质量。
三、铸造用原材料的质量优异与否。若是 金属炉料、溶剂、变质剂或者涂料等材料质量达不到标准,则会使得铸铁件产生气孔、夹渣、粘砂等缺陷,从而影响铸铁件的内部和外观质量。
四、工艺操作规程要合理。在制作铸件的时候,要不断提高工人的技术水平,与此同时,制定合理的工艺操作规程,使生产过程正确合理。
泊头市东建铸造有限责任公司(http://www.dongjianzhuzao.com)是 以阀门球铁铸件、机床床身铸件、合金铸件、消失模铸造为主的大型铸造、加工生产企业,对产品质量高标准严要求。