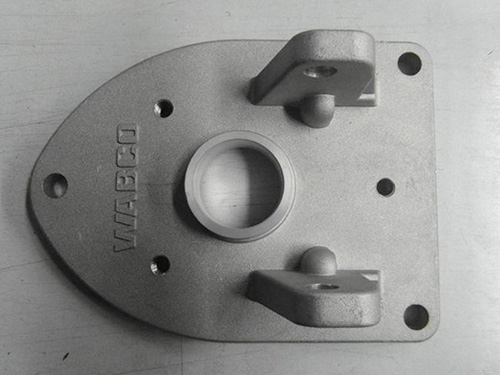

低压铸造的第三个步骤就是低压铸造的工艺过程本身,在这个步骤中,首先要进行的是一些铸造前的准备工作,例如对模具进行检查、喷砂、喷涂料、预热、模具的上下机等,这些看似简单的工作如果不仔细操作,依然后带来后期很大的麻烦。铝压铸件检查的内容通常包括产品编号、模具编号、侧模、模芯的偏距,刻字等是否和图纸、参数表、生产计划等;喷砂是一种对模具进行清理的过程,使模具达到表面无残余涂料、油污、脏物的要求;喷涂料是在模具型腔中喷涂特种涂料,避免铸造的铝合金材料对模具型腔造成污染、腐蚀以及后期逐渐粘连在型腔内不易脱模等不良后果;预热是将模具提前加热到预设的温度,以便喷涂料中的挥发成分能够完全挥发以及对型腔的尺寸进行精确保证,进而对铸件的尺寸型号进行精确控制。
第四个步骤就是铸造本身,也就是开始作业以铸造精确的铝合金车轮。在这个过程中,首先是对充分预热的模具进行加热,到达设定温度后等待下一步操作;将处于保温炉中的铝合金液体通过陶瓷升液管浇铸到型腔当中,当然,这之前对于铝合金液体成分和均匀度的测定十分重要。通常对于铝合金材料,较佳的浇铸温度为685~710℃,根据不同的工艺要求可以进行适当的调整。在保证铸件成形的前提下,浇注温度越低越好。浇注过程中,温度高越高则铝合金液体流动性越好,对轮毅的轮惘成形有利,但对轮辐的热节缩松倾向大,结晶晶粒也粗大,降低了轮毅的机械性能。当然,也不能过份地降低浇注温度,否则轮毅下部分的轮惘会过早凝固,失去压力下结晶的机会,最终影响产品质量。
然后一个大的步骤是对浇注的金属液体进行保压冷却,并且保压时间的长短完全取决于铸件的结构、铸型条件等实际因素,除了要考虑热节的因素之外,还应该考虑浇口的温度条件,这涉及到了热节的顺序凝固条件,浇口一定要保证比热节后凝固,如果浇口先凝固,或作为通道的轮辐先凝固,轮毅的热节处就会出现缩松。如果保压时间太长,容易冻浇口。浇口的保温是延长保压时间的关键。铸件经过一定时间的保压冷却以后成型,设计结晶的部分在实际条件下进行结晶,并且按照设计的热节冷却顺序逐渐冷却,轮盘中心部分的浇口然后冷却以后并且整个逐渐完全冷却后,开模进行脱模,一个铝合金车轮铸件的生产过程就完成了,经过后续的处理和严格的质量监测以后,整个产品就可以按照要求进行包装发货了。
泊头东固模具制造有限公司(http://www.hbdgmj.com)主营项目:压铸件流动性好,易熔焊,钎焊和塑性加工,在大气中耐腐蚀,残废料便于回收和重熔;但蠕变强度低,易发生自然时效引起尺寸变化。大型铝铸件零件加工变形的原因很多,与材质、零件形状、生产条件等都有关系。铝铸件加工表面应光洁、平正、铸字标志应清晰,浇、冒口清理后与铸件表面应齐平。 汽车铝配件对于边盖类薄壁零件,采用钣金冷做校正;容易磨损的轴孔类零件可采用金属喷镀、焊修、胶粘、机械加工等工艺以达到原厂尺寸。