1.加入孕育剂进行孕育处理
2.球墨铸件流动性较差,收缩较大,因此需要较高的浇注温度及较大的浇注系统尺寸,合理应用冒口,冷铁,采用顺序凝固原则
3.进行热处理
4.严格要求化学成分,对原铁液要求的碳硅含量比灰铸铁高,降低球墨铸件中锰,磷,硫的含量
5.铁液出炉温度比灰铸铁高,以补偿球化,孕育处理时铁液温度的损失
6.进行球化处理,即往铁液中添加球化剂
球墨铸件的防腐直接关系到管道的长期的使用性和性,因此是衡量管网技术及运行状况的一个重要指标。因铸铁中存在石墨,球墨铸件中的石墨以球状形式存在,并不影响基体材料的力学和机械性能,但据10个典型城市结果显示,我国城镇供水管网静漏失率达到12~13%,远远超过了要求城市漏失率控制在6%以下的标准,所以管道防腐一直是我们当前一个热门的课题。
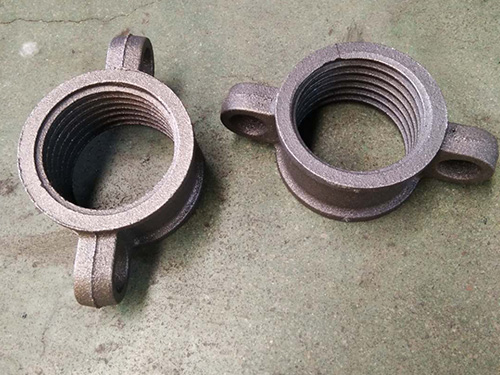
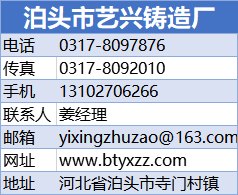
[一]、球墨铸铁生产工艺
凝固过程体积变化和压力损失是铸件缩松缺陷产生的直接原因。由于球墨铸铁的凝固过程既有金属液态收缩又有石墨化膨胀,既有初生阶段体积变化又有共晶阶段体积变化,所以球墨铸铁缩松产生的机理研究更显复杂。虽然有学者对球墨铸铁凝固过程的体积变化作了大量研究,但由于试验条件和方法不同得出的结论不甚一致。提出的体积变化计算模型(动态膨胀收缩叠加法)综合考虑了球墨铸铁凝固过程中的各个阶段,可以比较准确得出体积变化。凝固过程压力损失目前还没有准确计算模型。
但是将压力项引入到铸件缩松预测判据中,且得到比Niyama判据更精确的缩松预测图形。这充分说明凝固过程压力损失是缩松产生的主要因素之一。球墨铸铁体积变化和压力损失由球铁铸件生产的工艺决定。影响缩松产生的主要工艺因素有化学成分、孕育程度、模数及铸型强度等。
残余镁量高时,球铁缩孔缩松倾向大的观点已经得到普遍认同。缩孔缩松缺陷的形成,主要与镁在组织中分布不均和较大白口倾向有关。镁主要富集于珠光体和碳化物中,而该区是成分偏析和共晶凝固的最后区域,也是缩孔缩松危发区,镁的偏析,尤其是镁夹杂的富集为缩孔缩松形成创造了条件。
[二]、球墨铸铁表面处理工艺
1、表面淬火和激光热处理
若要在球墨铸铁件表面获得比较高的硬度而心部仍保持一定韧性可采用表面淬火处理的方法。表面淬火处理方法很多,可以是高频感应加热淬火也可以是火焰加热淬火和激光加热淬火等。具体工艺与整体淬火差不多:将球墨铸铁件表面加热到860~900℃,保温一段时间让表面组织全部奥氏体化后再在油或熔盐中冷却实现表明淬火,然后在250~350℃加热保温回火,以使表面组织转换为回火马氏体及残留奥氏体组织,表面组织中的原球状石墨形态不变。处理后的铸件表面具有较高的硬度,心部仍具有一定的韧性。
激光表面热处理除激光加热淬火外,还可在球墨铸铁件表面上实现激光相变硬化、激光冲击硬化等以提高球墨铸铁件的表面硬度。
2、表面化学处理
若要在球墨铸件表面获得非常高的硬度而心部仍保持一定韧性还可采用表面化学处理的方法。球墨铸铁的表面可进行渗氮、渗硼、渗硫以及低温气体碳氮共渗等,现用的比较多的是渗氮和低温气体碳氮共渗。渗氮前一般需要对球墨铸铁件进行退火、正火等预处理,然后用氨作为介质进行二段氮化处理。第一阶段氨分解率20%~35%,保温一段时间后将氨分解率提高到45%~55%,保温后炉冷至200℃出炉空冷,经过处理后球墨铸铁件表面硬度可达900HV,脆性2级。低温气体碳氮共渗同样可以明显提高球墨铸铁件表面的硬度和耐磨性,共渗温度一般为530~570℃,共渗介质为甲酞胺或三乙醇胺50%+乙醇50%。由于球墨铸铁中的碳和硅等元素比较多,可在共渗介质中再添加NH4Cl和TiH2;NH4Cl和TiH2有催渗作用,能加速球墨铸铁的共渗过程。
泊头市艺兴铸造厂(http://www.btyxzz.com)主要产品有搅拌机配件、灰铁铸件、减速机齿轮、机械加工、数控车床加工等业务。