外壳由金属和陶瓷部件构成气密结构腔体,电路基板和芯片通过后封装工艺装架在外壳内部,提供机械支撑、气密保护、内外电路连接、光电信号转换等功能,光通信器件的电信号和光信号通过外壳的输入输出端口传输,耗散的热量通过外壳传导到外壳外部。
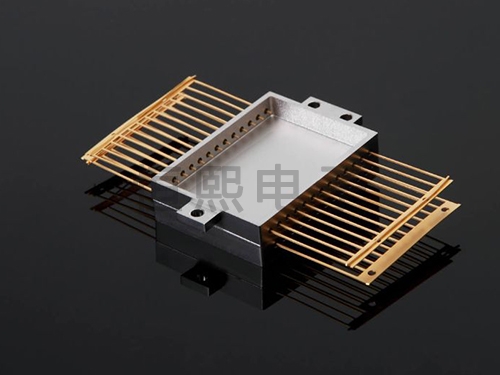
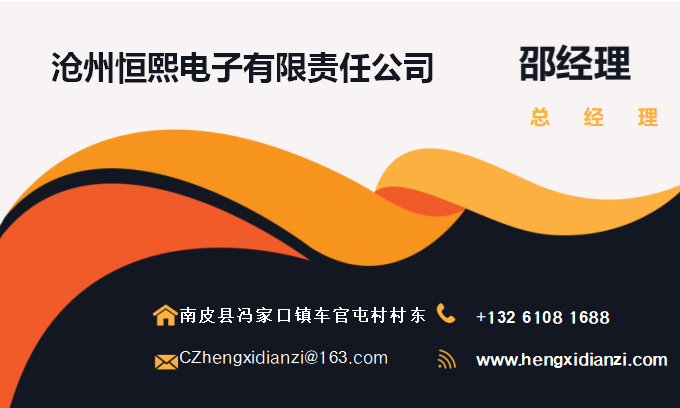
一、金属封装外壳的结构设计要求
TR组件目前常用的高功率发热芯片主要有GaAs,GaN和LTCC,其中典型的整体封装外壳TR组件的几乎都为封闭式盒体结构。GaAs,GaN芯片直接或间接(有过渡层)焊接在壳体上,然后和印制板进行键合,然后整个盒体进行密封装。
该种形式TR的气密封装形式简便,但是厚度受限,一般不低于5mm。我所目前常用微波、毫米波TR组件主要是Ku,K,Ka频段,半波长在5~11毫米。当TR组件的厚度受限时,就采用局部气密封装的形式,将天线和TR做成LTCC然后将LTCC焊接在TR背板上,对LTCC进行局部气密封。
相控阵毫米波导引头TR组件由于厚度受限,设计采用局部气密封装方式。相控阵毫米波导引头天线的间距为9mm,TR组件封装外壳典型结构为间距9mm的砖式结构。双面焊接LTCC基板,单面焊接2片,该TR背板上要同时集成LTCC及收发电路,中间还有部分波导,尺寸小,器件集成度高,安装定位要素多,精度要求高。该TR背板不仅是所有元器件的安装载体,也是整个TR抵抗环境应力破坏的基体,对设计该背板的材料除应与LTCC进行热匹配外,还应有足够的强度抵抗冲击、振动等环境因素的破坏。
为了与芯片的热膨胀系数相匹配以减少工作时芯片受热应力破坏的可能,应根据芯片的热膨胀系数选择与之相近的硅铝合金复合材料,硅铝合金复合材料的导热系数目前外洋有5,6,7,9,11,13,15,17等规格,国内厂家的产品还不能全部覆盖外洋的规格。由于加工性能和采购周期的限制,结合对国内相关使用情况的调研结果,对膨胀系数为9和11两种规格的材料进行了相关的验证。从试验结果来看,膨胀系数为9和11的硅铝合金复合材料材料LTCC封装的TR组件壳体的要求
除上述电路总体要求外,由于相控阵毫米波导引头项目TR组件外壳采用新型封装材料硅铝合金复合材料为基体材料,因其高脆性特点,结合气密封装性与环境适应性要求,结构设计需保护其加工工艺性、镀覆性能、焊接性能以及使用性能等。
二、蝶形微波器壳体生产工艺流程
传统的铝合金蝶形微波器壳体生产工艺流程包括9道工序,各工序分别为开卷、落料、切断废料、一次折弯、二次折弯、冲孔、攻丝、放置铆螺母、冲压铆螺母。在传统生产工艺中,各个工序之间很难实现自动化生产,需要工人来对蝶形微波器壳体的各个工序进行人工衔接,故在传统的铝合金微波器壳厂房内通常有一条长输送带,输送带完成各个工序之间的蝶形微波器壳体的半成品的输送工作,但输送带无法将蝶形微波器壳体的半成品放置到下一个工序的工作位置,还需要工人徒手操作将蝶形微波器壳体的半成品放置到该工序的工作位置。这种生产方式占地面积大,工作环境差,对工人依赖性大,效率低。
目前许多公司引进机械手来代替人工操作,由机械手来完成零件在各工位间的输送工作,生产工艺也发生了变化。改进的工艺流程包括9道工序,各工序分别为开卷、落料、切断废料、一次折弯、二次折弯、冲孔、攻丝、放置铆螺母、冲压铆螺母。铝合金卷材先经过开卷机进行开卷矫平,然后输送到落料工位进行落料,当运动一个工位以后,切断机切断废料;机械手开始工作,从落料工位将落料好的铝合金板材抓取出来,放到一次折弯工位,这时机械手释放落料好的铝合金板材,回到落料工位等待抓取一块落料好的铝合金板材;此时一次折弯处的冲压机开始工作,冲压完成后,机械手工作,此时一次折弯处的冲压机开始工作;冲压完成后,机械手工作,将冲压好的铝合金板材抓取到二次折弯工位,到位后,二次折弯设备开始工作,其他工序依次运行,较后加工完成电源加工。
沧州恒熙电子有限责任公司(http://www.hengxidianzi.com)主营多种不同型号的晶振外壳、电源外壳、金属封装外壳,配备镀金、镀镍、镀锡、电泳漆、阳极氧化等表面处理加工车间、全部实现本厂自主生产加工能、缩短交期等问题。产品远销北京、上海、广州、深圳、西安、等地。