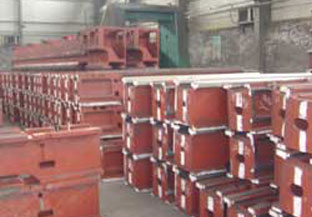
补焊时易出现裂纹
(1)冷裂纹当焊缝为铸铁型时,易出现冷裂纹。大型机床铸件裂纹发生时常伴随着可听见的较响的脆性断裂声音,焊缝较长或补焊刚性较大的缺陷时,常发生这种裂纹。其产生原因是 :焊接过程中由于焊件局部不均匀受热,焊缝在冷却过程中受到很大的拉应力,由于铸铁强度低,400℃以下基本无塑性,当拉应力超过铸铁的抗拉强度时,即发生冷裂纹。当焊缝中存在白口铸铁时,由于白口铸铁的收缩率((2.3)比灰铸铁的收缩率(1.26%)大,故焊缝更易出现冷裂纹,特别是 当焊缝强度大于母材时,冷却过程中母材牵制不住焊缝的收缩,结果在结合处母材被撕裂,这种现象称为“剥离”。当焊接接头刚性大、焊补层数多,补焊金属体积大,使焊接接头处于高应力状态时,如焊缝金属的屈服点又较高,难于通过其塑性变形来松驰焊接接头的高应力,则焊接裂纹易于在热影响区的白口区或马氏体区产生,形成热影响区冷裂纹。
(2)热裂纹当采用镍基焊接材料(如Z308,Z408,2508焊条)及一般常用的低碳钢焊条焊补铸铁时,焊缝金属对热裂纹较敏感。产生原因是 :采用镍基材料补焊铸铁时,由于铸铁含硫、磷高,形成较多的低熔点共晶物,如Ni-Ni3SZ(熔点644℃),Ni-Ni3P(熔点880℃),易产生热裂纹;采用低碳钢焊条焊补铸铁时,由于熔合比增大,母材中的碳、硫和磷大量熔入焊缝金属,形成大量铁的低熔点共晶体,同样易产生热裂纹回。
影响机床铸件质量的因素:
1、铸件的设计工艺性。由于灰口铸铁含碳量高,接近于共晶成分,故熔点比较低,流动性良好,收缩率小,因此适宜于铸造结构复杂或薄壁铸件。另外,由于石墨使切削加工时易于形成断屑,所以灰口铸铁的可切削加工性优于钢。进行设计时,除了要根据工作条件和金属材料性能来确定铸件几何形状、尺寸大小外,还得从铸造合金和铸造工艺特性的角 度来考虑 设计的合理性,即明显的尺寸效应和凝固、收缩、应力等问题,以避免或减少铸件的成分偏析、变形、开裂等缺陷的产生。
2、合理的铸造工艺。即根据大型机床床身结构、重量和尺寸大小,铸造合金特性和生产条件,选择合适的分型面和造型、造芯方法,合理设置铸造筋、冷铁、冒口和浇注系统等,以保证获得合格铸件。
3、铸造用原材料的质量。金属炉料、耐火材料、燃料、熔剂、变质剂以及铸造砂、型砂粘结剂、涂料等材料的直接影响铸件的质量。树脂砂、固化剂、涂料等,大大的减少和避免了机床铸件产生气孔、针 孔、夹渣、粘砂等缺陷,确保铸件外观质量和内部质量。
4、工艺操作,要制定合理的工艺操作规程。益恒铸业拥有高技术、高效率的铸造加工团队,对于各种类型的机床的铸造和加工拥有丰富的经验,制定和实施合理的工艺规程。
泊头市东建铸造有限责任公司(http://www.dongjianzhuzao.com)是 以机床床身由于灰口铸铁含碳量高,接近于共晶成分,故熔点比较低,流动性良好,收缩率小,因此适宜于铸造结构复杂或薄壁铸件。立车铸件均采用树脂砂、消失模实型铸造,单件达到40吨以上,年生产量在8500吨左右。包括床身、工作台、立柱、横梁、龙门顶、连接梁。树脂砂就是 把原砂和树脂混合后形成树脂砂,把树脂砂打入模具型腔中,通过加热或催化剂方法使其成型,成型后的坭芯再放入浇铸模具中进行浇铸。实型铸造是 将与铸件尺寸形状相似的石蜡或泡沫模型粘结组合成模型簇,刷涂耐火涂料并烘干后,埋在干石英砂中振动造型,在负压下浇注,使模型气化,液体金属占据模型位置,凝固冷却后形成铸件的新型铸造方法。