对机床铸件的性能要求主要有以下几个方面:
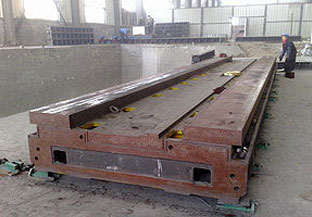
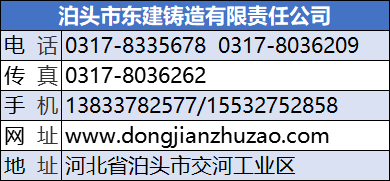
(2)良好的精度稳定性。
(3)高的弹性模量。
(4)良好的耐磨性。
(5)较好的减震性。
(6)良好的切削性能。
(7)良好的铸造性能。
(8)较高的尺寸精度,较低的表面粗糙度。
国内外生产机床铸件I要从化学成分、力学性能、金相组织、尺寸精度和时效处理等几方面进行控制。
采用数控机床加上零件时,要保证其较高的精度和加上初期、中期、后期尺寸精度的一致性,就要求铸件的硬度、加上性能的稳定。虽然数控机床有自动测量,刀具磨损自动补偿等功能,但铸件硬度与加上性能的波动大小仍会对加上精度的稳定性产生影响。实践证明,保持机床床身化学成分的稳定是 保证铸件硬度、加上性能稳定的重要措施。因此,熔炼铁液的C, Si, Mo含量(质量分数)波动均不应超过±0. 1%, C的波动范围为±0. 05%。
从使用角 度上看,机床铸件的刚性比其强度更重要,计算表明,即使达到机床较大切削力,高牌号铸铁件的抗压强度、抗拉强度仍有较大的安全系数,却会出现因其刚度差、抗变形能力不够而使强力高速切削的数控机床失去加上精度。因此,对现代数控机床铸件材质的刚性指标很重要,即灰铸铁的弹性模量越大,材质抗变形能力也越大。
铸铁弹性模量在强力切削下对数控机床保持精度的稳定性的作用越来越重要。弹性模量与强度有着密切的关系,强度越高,弹模量也越高。但不能以强度的测试来代替弹性模量的测试。因为即使是 同样的强度,弹性模数也有高低之分。熔炼配料中的废钢量,渗碳的机制,高温熔炼,孕育强化及化学成分中的Si/C比,以及金相组织中的石墨数量、大小等都是 影响弹性模量的重要因素。
超长床身的精加工过程中,在保证高加工精度及稳定性、提高生产效率方面还存在一些技术难点问题,主要为:
1)超长床身加工精度的稳定性;
2)超长床身加工过程中刀具的磨损;
3)主轴热变形对加工精度的影响;
4)超长床身导轨面高平行度的保证;
5)超长床身直线度的检测方法及检测数据的处理;
6)超长床身导轨高精度直线度的保证。
由于重型机床超长床身比较长,在精加工装卡过程中,很容易受重力的影响而变形,也极容易产生强压变形,导致加工后松开卡压时产生扭曲,无法保证加工精度的稳定性。
我们 采取的解决方法是 从床身毛坯划线开始,就严格控制床身的自由调平,粗加工、半精加工要求采用可调垫铁自由调平,使床身在自由状态下装夹、加工,这样在加工过程中产生的内应力也可以得到一定释放,从而减轻应力的积累,为精加工打下良好的基础。
在超长床身的精加工中,采用高度很低的调整垫铁多点位支撑,将调整垫铁以间隔1000-1200 mm沿床身均布。待多段床身临床整体拼装好后,在装卡过程中严格控制工件的调平工序,先将工件在自然状态下按已加工导轨面找平、找直后,抽纸检查各处垫铁受力的情况,由中间向两端对称的调实垫铁与床身底面的接触,再将压板压在调整垫铁的正上方,在压板周边床身上用百分表定表监测,将压板压紧,保证压板紧固前后百分表读数无变化。大型机床铸件采用这种装卡方法不但可以保证床身在全长范围内找正紧固后仍处于自由受力状态,不存在由于卡压而造成变形,有效的保证了工件的自由调平,而且垫实可靠,切削过程中不会发生振动,加工质量极其稳定。
泊头市东建铸造有限责任公司(http://www.dongjianzhuzao.com)是 以床身铸件由于灰口铸铁含碳量高,接近于共晶成分,故熔点比较低,流动性良好,收缩率小,因此适宜于铸造结构复杂或薄壁铸件。立车横梁铸件均采用树脂砂、消失模实型铸造,单件达到40吨以上,年生产量在8500吨左右。包括床身、工作台、立柱、横梁、龙门顶、连接梁。树脂砂铸件就是 把原砂和树脂混合后形成树脂砂,把树脂砂打入模具型腔中,通过加热或催化剂方法使其成型,成型后的坭芯再放入浇铸模具中进行浇铸。实型铸造是 将与铸件尺寸形状相似的石蜡或泡沫模型粘结组合成模型簇,刷涂耐火涂料并烘干后,埋在干石英砂中振动造型,在负压下浇注,使模型气化,液体金属占据模型位置,凝固冷却后形成铸件的新型铸造方法。