一、机床床身标准:GB9439—88
二、床身的特点:
(1)耐磨性与消震性好。由于铸铁中石墨有利于润滑及贮油,所以耐磨性好。同样,由于石墨的存在的消震性优于钢。
(2)工艺性能好。由于灰口铸铁含碳量高,接近于共晶成分,故熔点比较低,流动性良好,收缩率小,因此适宜于铸造结构复杂或薄壁铸件。另外,由于石墨使切削加工时易于形成断屑,所以灰口铸铁的可切削加工性优于钢。本厂还生产机床床身,大型铸件,立车铸件等各种大型铸件产品。
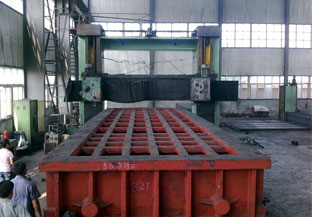
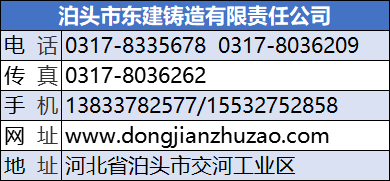
现代自动化机床铸件生产线由其特点决定了有以下特征。
大型化:机床铸件的生产要求流程复杂,从造型、浇注直至清理,从几公斤直至成吨的铸件全部由自动化来完成,要求设备向大型化发展。大型化设备可以提高劳动生产率,节约材料和投资,降低生产成本,同时也有利于新技术的推广和应用,适用了现代化工业大生产的需要。目前,设备的容量、重量、功率都明显地向大型化方向发展,几百米长的生产线己屡见不鲜,并且是空中、地上、地下同时作业。
高速化:传统的铸造工艺中一个铸件的生产工序相当漫长,从造型到熔化直至合格铸件的要几天时间,效率较低,现代的铸造自动线速度已超出了一般人的想象,在上世纪七、八十年代生产一个发动机缸体铸件还需1飞分钟,现已达到十几秒钟。
连续化和自动化:机床铸件设备的连续化、自动化可以提高生产效率,减轻劳动强度。特别是对劳动强度高、生产环境恶劣的铸造行业,这一点更为重要,现代的铸造设备已经从单机到简易联动到全自动化。利用各种提升机、气缸、皮带、辊子传输直至智能机器人的利用,大大减轻了操作者的劳动强度。
现代化机床铸件自动生产线的上述特点从诸多方面对其性能提出了不同要求,主要表现在:
生产能力:设备能力包括质量、数量方面的能力及对生产过程的适应能力。以数量表示的生产能力是由设备使用时的耐用度所决定的,又分为总的生产能力和周期性的生产能力;以质量表示的生产能力则是设备是否被投入使用的标准,反映在产品质量的标准、稳定性上:适应能力表示了设备对生产过程发生变化时的适应程度,是生产管理与设备管理一体化的标志。
机动性:所谓机动性是指设备是否能够,在多大程度上怎样以及在什么条件下被调整,以适应生产任务变化的需要。以数量表示的机动性是指设备通过使用时间或使用了强度的调整以适应产量变化的要求;质量上的机动性直接源自设备自身的质量;数量及质量指标调整的快慢可视为时间上的机动性;设备在其使用空间进行重新组合、安装、分类的可能性则反映了设备空间方面的机动性。
动态工作特性:在企业生产计划的范畴内,对于设备的经济寿命及维修计划的制订来说,表征设各能力的各项尺度并不是一成不变的。随着设备役龄的增加,其磨损必然加剧,因而技术特性也将发生变化。动态工作特性表明在上述条件下设备的各项性能指标将以何种形式,什么样的速度发生变化的特性。
投入、产出关系:现代设备的特征决定了它的资金密集、技术密集的特性。购置一台大型现代设备往往需投资数百万乃至数千万元,使用过程中,获取设备投入、产出方面的信息,是必不可少的。
对设备管理部门,利用率指设备的运转效率,指有效运转时间与设备运转时间的比率。
设备利用率是一种纵向延伸的指标,考核它可以反映设备运转情况和熟练程度以及设备系统功能的投入及性能发挥的状况,考核最终目的在于提高设备的利用效果,充分发挥设备的能力和潜力。
可靠性工程及设备开动率等都是对自动化生产线的评价方法。其中瑞典人威布尔提出了威布尔分布规律,主要适用于因疲劳和磨损而失效的系统。可靠性工程强调对设备管理量化分析,它应用概率论、数理统计方法为设备管理提供了科学的、量化的依据。在设计阶段,可应用可靠性工程预测不同方案的可靠度,进行择优处理;在使用阶段,则可分析设备系统的故障规律,对不同的维修策略进行优化选择。
国内外对于大型机床铸件的铸造自动化生产线的综合评价及考评体系的论述相对较少,多数沿用传统设备的考评方法,对此类设备的特殊性认识不足。在考评体系多采用各功能指标单项评价的方法。单项考评的弊端在于其对于单项设备是适用的,例如设备的完好率、开动率及有效度等指标。对于单机设备,单独的一项设备完好率指标就可以包涵了较多的考核项目,也能满足设备管理的要求,并达到最终的管理效果,但对于连续化、工序工位较多的铸造自动化生产线,此类考核评价有极大的片面性,容易产生考核的失真。
对于二维评价指标体系来讲,发展了一步,强调了指标权重,但二维评价指标体系只考虑了生产线的可动率和利用率。这其实是只考核了效果的指标,并没有对设备的管理过程进行考核。同时对于复杂的生产线来讲,考核的范畴也相对较少。
可靠性工程中的威布尔分布规律,主要强调了因疲劳和磨损而失效的情况,侧重于对运行部位、零部件的考核。可靠性中的设备量化分析重点强调了设备运行中的性能指标,并侧重于设备的可利用率和设备开动率。