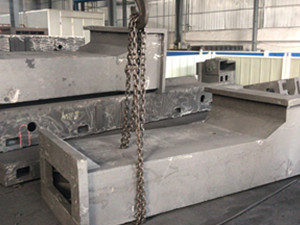
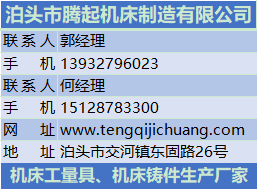
在实际的机床铸件铸造生产过程中,经常由于数控机床铸件结构方面的原因及工艺处理不合理而造成热裂、某些部位存在残余应力或残余变形,如板形件产生翘曲,半圆形铸件产生扩口等现象。严重影响铸件质量和使用寿命,给工业产生带来巨大经济损失。许多铸造缺陷都与凝固过程中的热应力的产生与发展有关。机床铸件凝固过程中各处冷却不均匀及砂型的阻碍作用,造成热应力和变形,结果产生热裂或在落砂后铸件中仍存在较大的残余应力和残余变形,对铸件的形状、尺寸精度和使用性能有很大影响.对铸件凝固过程的应力场模拟可以更好地了解铸件凝固过程中应力和变形的动态变化,在此基础上研究和预测热裂,并对铸件进行残余应力和残余变形分析,进行尺寸和精度分析,对实际生产提供科学指导。
实际生产中,大型复杂球铁机床铸件常采用无冒口铸造成型,由均衡凝固理论可知,在凝固过程中,由于球铁共晶凝固温度范围较宽(糊状凝固),冒口中的金属液很难对其进行充分补缩,主要利用球铁在共晶凝固阶段石墨化膨胀的特性,实现补缩,得到质量健全的球铁铸件。而实际生产创造均衡凝固的条件,必须满足:合金液大流量的快速浇注;采用冷铁强烈激冷形成坚固的铸型及泥芯;内浇口及出气冒口必须先于铸件凝固防止铁液回流:内浇口沿铸件圆周均匀分布径向引入,使铸型内温度场温度均匀。出气冒口减少充型阻力,加快液流的充型速度,有利于合金液大流量的快速浇注。冷铁在一定程度上对充型过程有阻碍作用,并且冷铁强烈激冷形成坚固的铸型,对采用无冒口铸造生产提高大型复杂球铁铸件滑枕的质量十分有利。从上述三种方案的总充填时间和内浇口充型平均速度来看,不同方案的内浇口平均充型速度有明显差异,总充填时间相差不大,内浇口平均速度的增加,并没有引起总充型时间减少。通过对三种方案的充型过程进一步研究,另发现充型时间与铸件的结构特点有很大联系。大型机床铸件内腔复杂,且在铸件四周不对称位置分布着10个尺寸大的孔或槽,在设计浇冒系统过程中使用砂芯,而砂芯在一定程度上引起金属液回流,使金属液向下流动或给下一时刻的自由表面施加一个反向速度,充型速度急剧降低;另铸件壁厚薄不均匀,整个铸件的9个较深厚大断面也对总充型时间有一定影响,当金属液充满厚大断面进入相对较小断面时,此时速度剧增,且厚大断面越深,充型速度越大,遇到砂芯后的回流现象也越严重,铸件整个充型过程不平稳,从而使得总充型时间并没有得到相应的减少。
泊头市腾起机床制造有限公司(http://www.tengqijichuang.com)是一家致力于机床量具、机床铸件产品生产、销售为一体的现代化企业。可定做各类机床床身铸件、机床滑枕铸件、机床导轨铸件等,产品远销多个省、市、自治区。