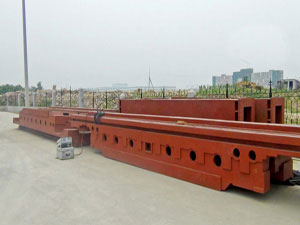
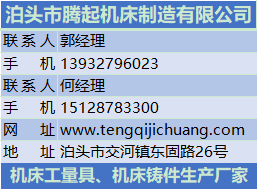
因铸件外形尺寸很大,长度达到近4米,宽度、高度均接近半米。所以我们在设计及生产中采用砂型铸造,并且型芯采用树脂砂铸造。(树脂砂适用在球墨铸铁上,用的效果比较好,尤其是大件,其优点是不粘砂,表面质量好。铸造缺陷也少,废品率低。)树脂砂芯用树脂砂制造的各种型芯。型芯在芯盒内硬化后再将其取出,能保证型芯的形状和尺寸的正确。
机床铸件属大断面球墨铸铁件,壁厚面大会导致铸件的凝固冷却速度缓慢,共晶转变时间长,由此而造成的组织特点是石墨数量少,石墨的形状差,易出现碎块状石墨,基体中易产生铁素体,成分偏析严重,由于化学成分偏析所产生的碳化物,经长时间的热处理也难以消除,并导致晶粒粗大、缩松和黑斑等缺陷的出现。由上述原因,铸件的力学性能内外相差大,性能总体水平低,且波动较大。实际生产中,如浇注方式采用卧浇,则不利于液流快速充填,同时面朝上的大平面易出现夹砂等缺陷;采用斜浇,布置组合型芯成形铸件复杂腔体时,存在型芯定位、测量以及其它技术难题;立浇底注是最常用的浇注工艺,但铸件顶部布置高压油孔的厚大部位易出现夹渣、缩孔、缩松等铸造缺陷,大型机床铸件质量仍不能满足实际生产要求。
大型复杂球铁铸件滑枕在实际生产中采用无冒口铸造,半封闭式浇注系统,立浇底注(高压油孔的厚大部位布置在铸件顶部),树脂砂造型,顶部增设小出气冒口观察金属液是否充满,底部安放冷铁,涂料采用水基石墨涂料(外)与错英粉涂料(内)。对滑枕的铸造工艺进行设计,再以实际生产滑枕铸件的几何尺寸和工艺方案为设计依据对充型过程进行数值模拟研究。通过合理优化浇冒口、出气孔及对充型过程进行温度场、流场、应力场等分析,获得生产良好铸件的铸造工艺参数。
考虑设计的滑枕这类数控机床铸件体积较大,而且要求在一顶端面没有缺陷,以便于油道的铺设与运作正常不漏油。在卧浇时对于型芯要求较高,处于悬空状态,不利于定位,而且在浇注时卧浇时最后的凝固面在一侧的大面上,这样就不能很好的保证顶端面的工艺要求;而在立浇时,采用半封闭式浇注法,由底部使用雨淋式底部注入法,来保证顶端的无缺陷要求,同时可以在顶端面设置冒口,在模拟时可让所产生的缺陷最终集中于冒口的残余废料中去,这样则保证了所要求的无缺陷铸件顶部油道部分。
泊头市腾起机床制造有限公司(http://www.tengqijichuang.com)是一家致力于机床量具、机床铸件产品生产、销售为一体的现代化企业。可定做各类机床横梁铸件、机床滑座铸件、机床导轨铸件等,产品远销多个省、市、自治区。