布袋除尘器的阻力是 指气流通过布袋除尘器的流动阻力,当除尘器进出口截面积相等时,可以用除尘器进出口气体平均静压差度量。
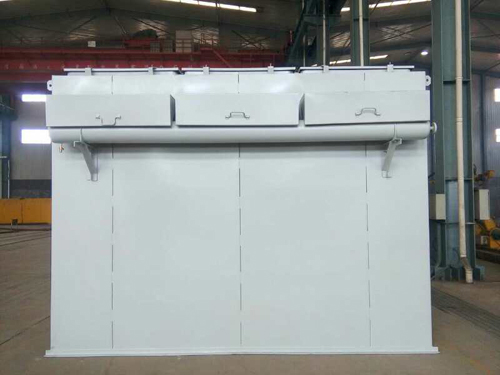
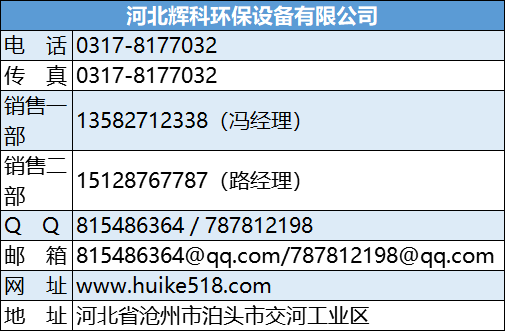
由于阻力与流速的平方成正比,故降低气体流速更为有效。降低速度的关键是 进出风口,进出口气流速度高,降速潜力大。
滤袋阻力与滤料的结构、厚度、加工质量和粉尘的性质有关,采用表面过滤技术(覆膜、超细纤维面层等)是 防止粉尘嵌入滤料深处的有效措施。
滤袋使用后,粉尘渗透到滤料内部,形成“深度过滤”,但随着运行时间的增长,残留于滤料中的粉尘会逐渐增加,滤料的阻力也会显著增大,较终会形成堵塞,同时也意味着滤袋寿命终结。
脉冲单机除尘器在运行过程中要防止粉尘进入滤料纤维间隙,如果出现糊袋(烟气结露、油污等)则过滤状态会更加恶化。一般情况下,滤料阻力长时间保持小于400Pa是 理想的状况。如果保持在600~800Pa也是 属于正常的状态。
滤袋清灰后,残留在滤袋内部的粉尘残留阻力也是 除尘器过滤的主要能耗。残留粉尘阻力大小与粉尘的粒径和粘度有关,特别是 与清灰方式、滤袋表面的光洁度有关。在保障净化效率的前提下,应尽量减小残留粉尘的阻力,相关措施如下:
(1)选择强力清灰方式或缩短清灰周期,并保证清灰装置正常运行。
(2)强化滤料表面光洁度,如研光后处理。或采用表面过滤技术,如使用覆膜滤料、超细纤维面层滤料。
(3)粉尘荷电,改善粉饼结构,增强凝并效果。
堆积粉尘层阻力大于等于定压清灰上下限阻力设定压差值,清灰前粉尘层阻力达到较大值,清灰后粉尘层阻力降到较小值或零。除尘器型式和滤料确定后,堆积粉尘层阻力是 设备阻力构成中的可调部分。对于单机除尘器,粉尘层阻力反映了清灰时被剥离粉尘的量,即清灰能力和剥离率;对于大型布袋除尘器,则体现了每个清灰过程中被喷吹的滤袋数量。
堆积粉尘层阻力(即清灰上下限阻力设定差值)主要与粉尘的粒径、勃性、粉尘浓度和清灰周期有关。粉尘浓度低时,可延长过滤时间;当粉尘浓度高时,可适当缩短清灰周期。
刻意地追求低的粉尘层阻力是 不合适的,一般认为增加滤袋喷吹频度会缩短滤袋的寿命,但是 运行经验表明,除玻纤滤袋外,尚无因缩短清灰周期而明显影响滤袋使用寿命的案例。根据工程经验,粉尘层阻力选择200Pa为宜。
一般布袋除尘器的阻力由除尘器结构阻力、滤料阻力、滤袋粉尘残留阻力(初层)和堆积粉尘层阻力四部分组成,传统的布袋除尘器的结构阻力和滤料残留阻力较大,其节能的根本措施主要有:1)降低气流在除尘器内的流动速度并采取导流措施使气流合理运动,这样可以降低单机脉冲袋式除尘器的结构阻力;2)采用覆膜滤料和超细纤维高密面层滤料,可显著降低滤袋粉尘残留阻力和粉尘层厚度;3)合理的清灰周期和清灰强度可减少粉尘层厚度降低粉尘层阻力。
河北辉科环保设备有限公司(http://www.huike518.com)生产的产品中频炉除尘器加料时,通过加料设备进行加料,根据生产需要几次将料加满,解决了加料时烟气难捕集的问题;出钢时,中频炉平台翻转直接出到出钢轨道平车上的钢包里,出钢过程在烟罩内完成,克服了局部集尘罩出钢时烟气部分外漏的情况。铸造厂除尘器采用铸造冲天炉除尘器能否及时、有效吹落沾在整条布袋上的粉尘,保障正常工作是 这些部位所用除尘器(称之“砂处理除尘器”)发挥作用的关键。在储气容积、布袋尺寸、喷吹主管口径确定之后,选择脉冲气体的压力、喷吹嘴的口径、喷嘴至布袋口的距离以及喷吹的频次都是 至关重要的。打磨车间除尘器进风口处设置一导流板,用于防止含尘直接冲击滤芯,从而延长滤芯的适用寿命。木工除尘器用于木工车间,打磨车间,油漆车间的由管道、风机、过滤器组成的专用的除去加工过程中产生的锯末、油漆粉尘等颗粒的装置。